Durable Siding for Extreme Weather
Protecting your home from the ravages of extreme weather requires careful consideration of your siding. This guide explores the various durable siding options available, delving into their unique properties, installation techniques, and long-term maintenance needs. We’ll examine how different materials withstand high winds, heavy rainfall, snow, ice, and extreme temperature fluctuations, ensuring your home remains secure and aesthetically pleasing for years to come.
From fiber cement’s resilience to metal’s longevity and vinyl’s ease of maintenance, we’ll provide a comprehensive comparison, helping you make an informed decision based on your specific climate and budget. We’ll also cover crucial installation best practices, preventative maintenance strategies, and relevant building codes, equipping you with the knowledge to safeguard your investment.
Types of Durable Siding Materials
Choosing the right siding for your home, especially in areas prone to extreme weather, is a crucial decision impacting both aesthetics and longevity. The durability of your siding directly correlates with its ability to withstand harsh conditions like heavy rain, strong winds, extreme temperatures, and intense UV radiation. This section will delve into the properties and performance of various siding materials commonly used in such environments.
Comparison of Durable Siding Materials
Selecting the ideal siding material requires careful consideration of several factors. The following table provides a comparison of four popular choices: fiber cement, vinyl, metal, and engineered wood, highlighting their strengths and weaknesses concerning cost and performance in extreme weather.
Material | Pros | Cons | Cost Range (per sq ft) |
---|---|---|---|
Fiber Cement | High durability, fire resistance, pest resistance, low maintenance, paintable | Can be brittle, more expensive than vinyl, requires professional installation | $3 – $10 |
Vinyl | Low cost, low maintenance, variety of colors and styles, easy installation | Can be damaged by hail or impact, can fade in intense sunlight, less durable than other options | $1 – $3 |
Metal (Aluminum or Steel) | Extremely durable, resistant to fire, insects, and rot, long lifespan | Can dent, susceptible to corrosion (especially steel), can be noisy in high winds, expansion and contraction can cause issues | $2 – $8 |
Engineered Wood | Good insulation properties, aesthetically pleasing, relatively low cost | Susceptible to moisture damage, requires regular maintenance, shorter lifespan compared to other options | $2 – $5 |
Material Properties and Extreme Weather Resistance
The durability of each siding material in extreme weather is influenced by several key properties.Fiber cement’s strength comes from its composite nature—a blend of cement, cellulose fibers, and other additives. This creates a material resistant to impact, moisture, and fire. Its UV resistance is also good, preventing significant fading over time. However, it is susceptible to cracking under extreme stress.Vinyl siding’s affordability stems from its plastic composition.
While relatively water-resistant and easy to maintain, it lacks the impact resistance of fiber cement or metal. Prolonged UV exposure can lead to fading and embrittlement. Extreme temperature fluctuations can cause expansion and contraction, potentially leading to warping or cracking.Metal siding, particularly aluminum, offers superior durability and resistance to extreme weather. Its strength protects against impact damage, while its non-porous nature ensures water resistance.
Aluminum’s resistance to corrosion is also superior to steel. However, expansion and contraction with temperature changes need to be considered during installation.Engineered wood siding, often treated to resist rot and insects, offers a balance between aesthetics and cost. However, its susceptibility to moisture damage makes it less suitable for areas with frequent rainfall or high humidity. Proper sealing and maintenance are crucial to extend its lifespan in extreme weather.
Lifespan and Maintenance Requirements
The following table summarizes the expected lifespan and maintenance needs of each siding material under extreme weather conditions. These are estimates and can vary depending on the specific product, installation quality, and severity of the climate.
Material | Lifespan (Years) | Maintenance Requirements |
---|---|---|
Fiber Cement | 50+ | Periodic repainting (every 10-15 years), occasional repair of minor damage |
Vinyl | 20-30 | Cleaning as needed, repair of damaged panels |
Metal | 50+ | Periodic cleaning, occasional repair of dents or scratches |
Engineered Wood | 15-25 | Regular cleaning, repainting every 5-7 years, potential need for sealant reapplication |
Installation Techniques for Extreme Weather Resistance
Proper installation is paramount to ensuring the longevity and weather resistance of your durable siding. A well-installed siding system will protect your home from the elements for years to come, while poor installation can lead to costly repairs and damage. This section Artikels best practices for achieving optimal performance in extreme weather conditions.
Successful installation hinges on meticulous preparation, precise execution, and the use of high-quality materials. Ignoring any of these aspects can compromise the entire system’s integrity, particularly in areas prone to severe weather events such as hurricanes, blizzards, or intense rainfall.
Preparing the Underlying Wall Structure
Preparing the underlying wall structure is crucial for optimal siding performance. A solid foundation ensures the siding remains securely attached and prevents water penetration. This involves several key steps:
- Inspect and Repair: Thoroughly inspect the existing wall sheathing for any damage, rot, or insect infestation. Repair or replace any compromised areas using appropriate materials. This is especially important in areas exposed to direct sunlight, moisture, or wind.
- Moisture Barrier: Install a continuous moisture barrier, such as housewrap, over the sheathing. This barrier prevents moisture from penetrating the wall assembly and reaching the siding. Overlap seams according to manufacturer instructions, typically 6 inches minimum. Properly seal all penetrations, such as windows and doors, with compatible sealant.
- Leveling and Straightening: Ensure the wall sheathing is level and plumb. Any significant irregularities can lead to uneven siding installation and potential stress points. Use shims or furring strips to correct imperfections before installing the siding.
Flashing and Sealing Techniques
Proper flashing and sealing are critical to preventing water intrusion, which is a major cause of siding failure. Flashing redirects water away from vulnerable areas, while sealing prevents gaps where water can enter.
Consider a scenario where a home is located in a coastal region subject to frequent high winds and heavy rainfall. Without proper flashing around windows and doors, water could easily penetrate behind the siding, leading to rot and mold. The same applies to areas where the roof meets the wall. Thorough flashing and sealing in these high-risk areas are non-negotiable.
Illustrative Description: Imagine a window installation. Flashing should be installed behind the window frame, extending several inches beyond the frame on all sides. This creates a waterproof barrier that directs water away from the window and down the wall. Caulk or sealant should be applied around the perimeter of the window frame where it meets the siding, creating a watertight seal.
A similar process applies to doors, roof penetrations, and other vulnerable areas. Properly installed flashing will overlap with the next piece to create a continuous water barrier. For example, flashing around a window should overlap the flashing installed above the window, preventing water from traveling behind the flashing.
Best Practices for Siding Installation
Following best practices during installation maximizes durability and weather resistance. This includes:
- Start at a Corner: Begin installation at a corner, ensuring proper alignment and spacing between siding panels. Maintaining consistent spacing throughout the installation process is vital for a professional finish and even distribution of stress.
- Use Appropriate Fasteners: Employ fasteners designed for the specific siding material and climate conditions. Over-fastening can damage the siding, while under-fastening can lead to loose panels and water penetration. Fasteners should be driven straight and flush with the siding surface to prevent water accumulation.
- Proper Overlap: Ensure sufficient overlap between siding panels to prevent water penetration. Overlap should be consistent and meet manufacturer recommendations. This creates a barrier against driving rain and wind-driven moisture.
- Seal All Joints: Seal all joints and seams between siding panels and around accessories using a high-quality, weather-resistant sealant. This prevents water from entering the wall system and helps maintain a long-lasting installation.
- Inspect Regularly: Regularly inspect the siding for any signs of damage or deterioration. Promptly address any issues to prevent further damage and ensure the continued protection of your home.
Impact of Specific Weather Events on Siding Durability
Extreme weather events can significantly impact the longevity and aesthetic appeal of exterior siding. Understanding how different weather phenomena affect various siding materials is crucial for selecting appropriate materials and ensuring proper installation for long-term protection. This section will examine the effects of high winds, heavy rain, snow, ice, and extreme temperature fluctuations on common siding types, highlighting common failure points and recommending preventative measures.
High Winds and Siding Damage
High winds pose a significant threat to siding, particularly in areas prone to hurricanes or tornadoes. The force of the wind can dislodge poorly installed siding, causing damage to the underlying structure and leading to water infiltration. Materials like vinyl siding, while generally resistant to wind damage, can be compromised if not properly fastened. Wood siding, especially older or improperly maintained installations, is more vulnerable to wind damage, potentially resulting in warping, cracking, and even complete detachment.
Fiber cement siding, due to its weight and strength, offers superior resistance to high winds but still requires secure installation. Common failure points include improperly fastened panels, gaps between panels, and inadequate flashing around windows and doors. Wind-driven debris can also cause significant damage to all siding types.
Effects of Heavy Rain and Moisture
Prolonged exposure to heavy rain can lead to various problems depending on the siding material. Wood siding is susceptible to rot and water damage if not properly sealed and maintained. Vinyl siding, while resistant to water damage, can warp or buckle if water penetrates behind the panels. Fiber cement siding, being less porous than wood, is more resistant to water damage but can still suffer from water infiltration if the installation is faulty.
Metal siding generally handles heavy rain well, provided proper drainage is in place. Common failure points include inadequate caulking around windows and doors, damaged flashing, and gaps in the siding installation allowing water penetration.
Snow and Ice Accumulation
Heavy snow and ice accumulation can put significant stress on siding, especially in areas with steep roofs. The weight of the snow and ice can cause sagging, cracking, or even complete collapse of the siding. Wood siding, being more susceptible to expansion and contraction due to temperature changes, is particularly vulnerable. Vinyl siding can also be damaged by heavy snow loads, especially if the installation is not strong enough to withstand the added weight.
Fiber cement siding generally offers better resistance to snow and ice loads due to its strength and durability. Ice dams, formed by melting snow refreezing at the roofline, can cause significant water damage behind siding regardless of material.
Impact of Extreme Temperature Fluctuations
Significant temperature swings can lead to expansion and contraction of siding materials, creating stress and potential failure points. Wood siding is particularly susceptible to warping, cracking, and splitting due to these temperature changes. Vinyl siding, while less affected, can still expand and contract, potentially leading to gaps or buckling. Fiber cement siding exhibits relatively low expansion and contraction, making it more resistant to temperature fluctuations.
Metal siding, while generally stable, can be susceptible to expansion and contraction depending on the metal type and its coefficient of thermal expansion.
Preventative Measures for Extreme Weather
Weather Event | Preventative Measures |
---|---|
High Winds | Properly fasten siding to sheathing, use appropriate flashing around windows and doors, ensure adequate wind blocking in the wall assembly. |
Heavy Rain | Use quality caulking and sealant, install proper flashing, ensure good drainage away from the foundation, maintain good ventilation behind siding. |
Snow and Ice | Regularly remove snow and ice buildup, install ice and water shields under roofing, ensure proper attic ventilation to prevent ice dam formation. |
Extreme Temperature Fluctuations | Choose siding materials with low expansion and contraction rates, ensure proper installation to allow for movement, consider using expansion joints where appropriate. |
Maintenance and Repair of Durable Siding
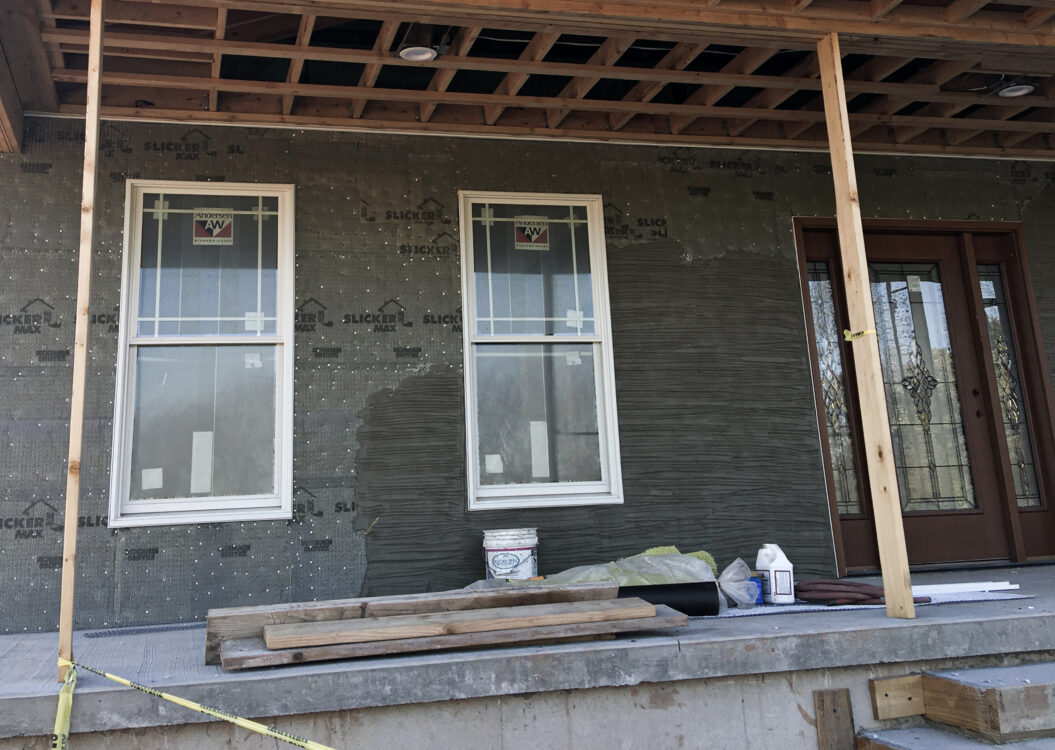
Proper maintenance and timely repairs are crucial for extending the lifespan of your durable siding and protecting your home from the elements. Regular inspections and preventative care can significantly reduce the need for costly repairs down the line, preserving both the aesthetic appeal and structural integrity of your home’s exterior. Neglecting maintenance can lead to accelerated deterioration, potentially requiring extensive and expensive repairs or even complete siding replacement.
Regular Inspection and Maintenance of Siding
A comprehensive inspection should be conducted at least twice a year, ideally in spring and fall. This allows for the identification of minor issues before they escalate into major problems. During the inspection, pay close attention to the following areas: Look for any signs of damage such as cracks, dents, loose or missing panels, warping, or discoloration.
Examine caulking around windows and doors for cracks or gaps, and check for any signs of water damage or insect infestation. Note the condition of flashing around chimneys and vents, ensuring it’s properly sealed and intact. Cleaning debris from gutters and downspouts is also essential to prevent water damage. Regular cleaning helps remove dirt, mildew, and other contaminants that can degrade siding over time.
Repairing Common Siding Damage
Minor cracks and dents in many siding materials can often be repaired with fillers specifically designed for the type of siding. For example, a small crack in vinyl siding can be filled with a vinyl-compatible caulk, ensuring a color match for a seamless repair. For larger cracks or holes, you may need to replace the damaged section. This often involves carefully removing the damaged panel and installing a new one, ensuring proper alignment and sealing.
Loose panels can usually be re-secured using appropriate fasteners, but if the underlying structure is compromised, further repairs may be necessary. Always refer to the manufacturer’s instructions for specific repair techniques for your siding material. For example, repairing fiber cement siding requires different techniques and materials than repairing vinyl siding.
Cleaning Methods for Different Siding Materials
Choosing the right cleaning method is essential to prevent damage. For vinyl siding, a simple solution of mild detergent and water, applied with a soft brush or sponge, is usually sufficient. Avoid abrasive cleaners or high-pressure washers, as these can damage the surface. For wood siding, a pressure washer can be used cautiously, but always test a small, inconspicuous area first.
Use a cleaner specifically formulated for wood to prevent damage and preserve the natural finish. For fiber cement siding, a similar approach to vinyl siding is recommended, using a soft brush and mild detergent solution. Always rinse thoroughly with clean water after cleaning to prevent residue buildup. For aluminum siding, a simple wash with soap and water is usually enough.
Avoid abrasive cleaners and harsh chemicals. Always test any cleaning solution on a small, inconspicuous area first to ensure it doesn’t damage the siding.
Building Codes and Regulations for Extreme Weather Siding
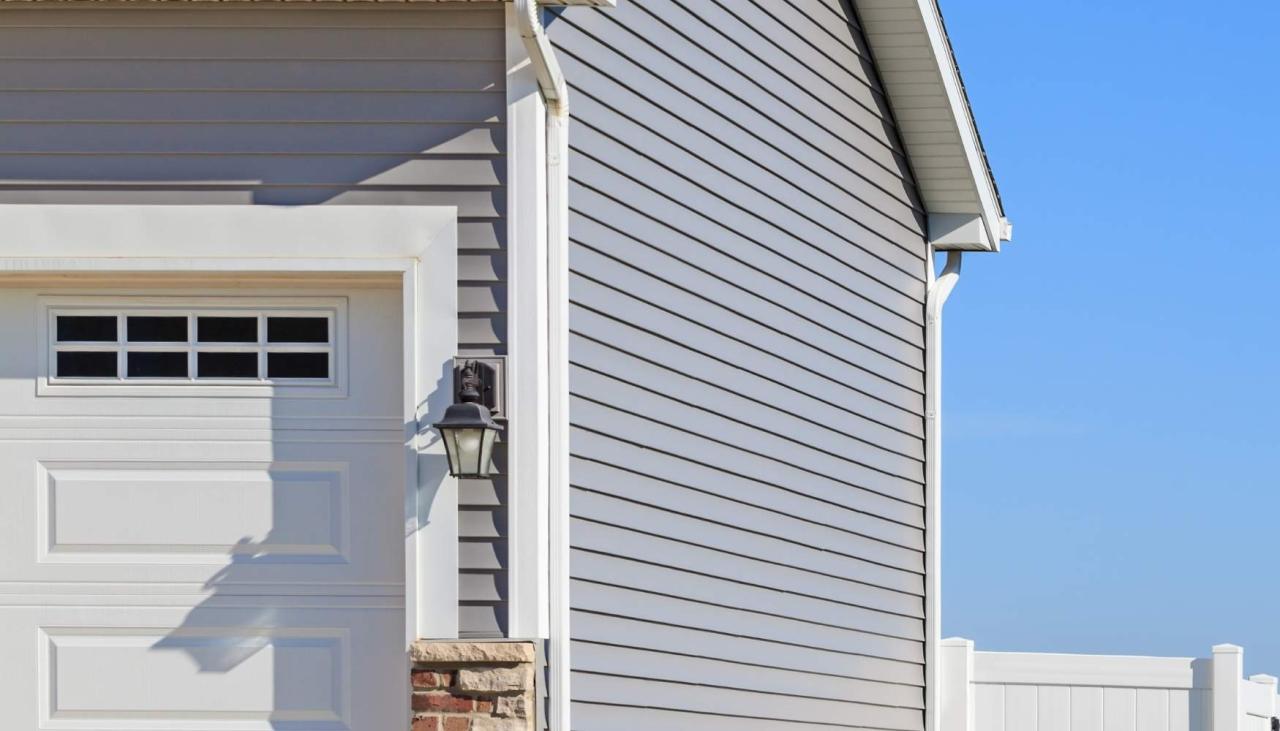
Building codes and regulations concerning exterior siding are crucial for ensuring structural integrity and safety, particularly in regions susceptible to extreme weather events. These codes vary by location and are designed to protect both property and inhabitants from damage caused by high winds, heavy snow, rain, and other severe weather phenomena. Compliance with these regulations is not merely a suggestion; it’s a legal requirement that directly impacts the safety and longevity of a building.The importance of using approved materials and adhering to specified installation procedures cannot be overstated.
Building codes often mandate the use of specific siding materials that have been tested and proven to withstand the forces of extreme weather. These materials typically meet certain performance standards for impact resistance, wind uplift resistance, and water resistance. Furthermore, the installation methods are meticulously Artikeld to guarantee a secure and durable bond between the siding and the underlying structure.
Improper installation, even with approved materials, can compromise the overall effectiveness of the siding and lead to significant damage.
Specific Code Requirements for Extreme Weather Siding
Building codes frequently stipulate minimum requirements for wind load resistance, ensuring that the siding can withstand high-velocity winds without detaching or causing structural damage. For instance, in hurricane-prone areas, codes might specify the use of impact-resistant siding materials and require stronger fastening methods to prevent wind uplift. Similarly, in regions with heavy snowfall, codes may address the need for sufficient ventilation behind the siding to prevent moisture buildup and ice damming.
These codes also often address the appropriate flashing and sealing around windows and doors to prevent water intrusion. Examples of specific code requirements can be found in the International Building Code (IBC) and local amendments thereto, which often include detailed specifications on fastener type, spacing, and penetration depth for various siding materials and weather conditions. Failure to meet these requirements can lead to costly repairs and potentially endanger the occupants of the building.
Consequences of Non-Compliance
Non-compliance with building codes regarding siding installation in extreme weather conditions can result in several serious consequences. These consequences can range from relatively minor issues, such as voiding building permits or insurance coverage, to far more severe problems. In the event of severe weather damage, non-compliant siding may fail, leading to water intrusion, structural damage, and even collapse of the building.
This can result in substantial repair costs, loss of property value, and potential injury or loss of life. Moreover, municipalities often enforce building codes through inspections and can issue fines or require remediation of non-compliant installations. Insurance companies may also refuse to cover damage caused by non-compliant siding, leaving homeowners to bear the entire cost of repairs.
A real-life example could involve a home with improperly installed vinyl siding in a hurricane-prone region. During a hurricane, the siding could be ripped off, causing significant damage to the underlying structure and leaving the home vulnerable to water damage. This scenario could result in substantial repair costs, and the homeowner might face legal ramifications due to non-compliance with building codes.
Cost Considerations for Durable Siding
Choosing durable siding involves a careful consideration of both upfront and long-term costs. While initial investment may vary significantly depending on the material selected, the overall cost-effectiveness is heavily influenced by factors like maintenance requirements, lifespan, and potential repair expenses. Understanding these cost components is crucial for making an informed decision that aligns with your budget and long-term goals.
Comparative Costs of Durable Siding Materials
The initial cost of siding materials varies considerably. A bar graph illustrating cost per square foot would show a range, with less expensive options like vinyl at the lower end and more premium materials like fiber cement and brick at the higher end. For example, vinyl siding might cost between $3 and $8 per square foot, while fiber cement could range from $8 to $15, and brick, due to its labor-intensive installation, could easily exceed $20 per square foot.
These are broad estimates, and actual costs will depend on factors like material quality, region, and supplier. A hypothetical bar graph would display these cost ranges visually, with each material represented by a bar whose length corresponds to its cost range.
Factors Influencing Overall Siding Installation Costs
Several factors contribute to the overall cost of siding installation. Labor costs represent a significant portion, varying based on the complexity of the project, the size of the house, and the contractor’s hourly rate. Materials, as discussed above, represent another significant expense, with prices fluctuating based on market conditions and material choices. Project complexity significantly influences cost.
A simple installation on a straightforward structure will be cheaper than a complex project involving extensive repairs, intricate designs, or difficult-to-access areas. Additional factors such as permits, waste removal, and potential demolition costs can also increase the overall expense.
Cost Savings from Durable Siding Materials
Investing in durable siding materials often leads to significant long-term cost savings. High-quality siding materials, such as fiber cement or engineered wood, require less frequent maintenance and repairs compared to less durable options like vinyl or aluminum. For instance, fiber cement siding, with its resistance to rot, insects, and fire, may eliminate the need for costly repairs or replacements that might be necessary with vinyl siding every 10-15 years due to fading, damage from impacts, or moisture damage.
The reduced maintenance needs and extended lifespan of durable materials translate into considerable savings over the life of the house, outweighing the higher initial investment in many cases. This long-term perspective is crucial when evaluating the true cost-effectiveness of different siding options.
Last Recap
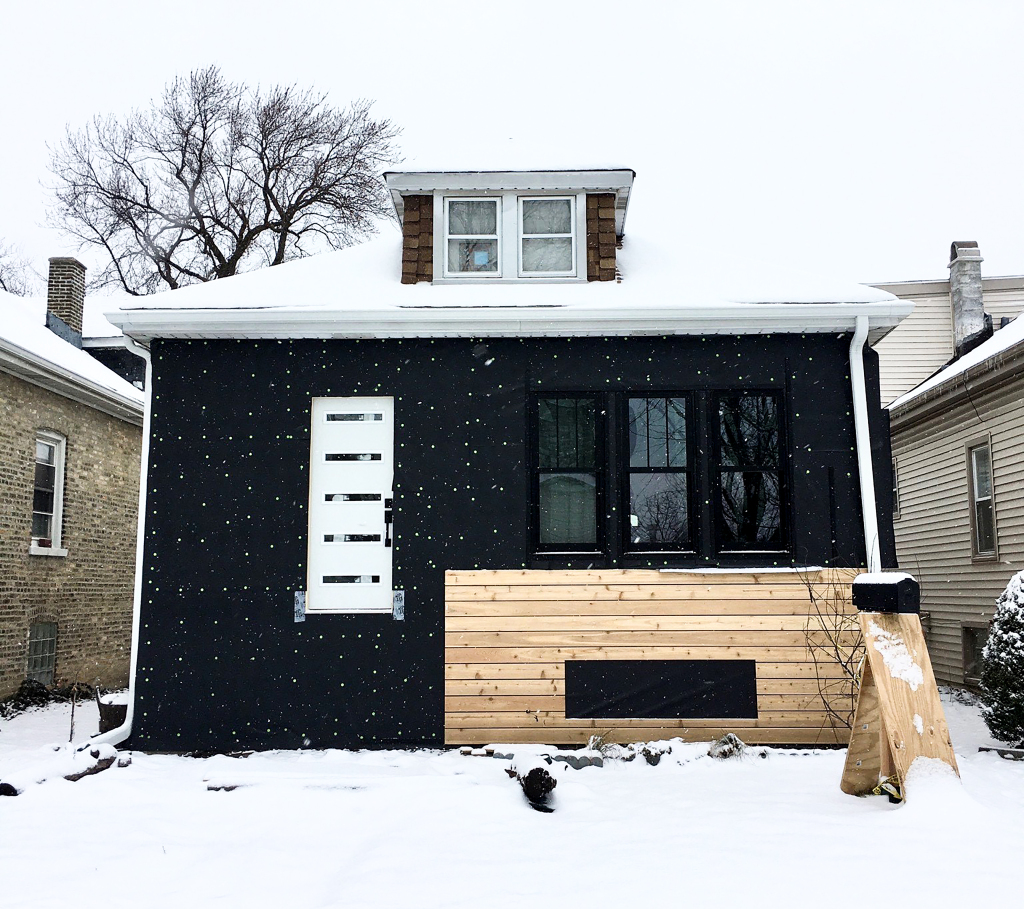
Choosing the right durable siding for extreme weather conditions is a crucial investment in your home’s protection and longevity. By understanding the properties of various materials, mastering proper installation techniques, and implementing regular maintenance, you can significantly extend the lifespan of your siding and safeguard your property from the elements. This guide provides a comprehensive foundation for making informed decisions, leading to a resilient and aesthetically pleasing exterior that stands the test of time.
Detailed FAQs
What is the average lifespan of durable siding?
The lifespan varies greatly depending on the material and climate. Fiber cement can last 50+ years, vinyl 20-30 years, and metal even longer, potentially exceeding 50 years with proper maintenance.
How often should I inspect my siding?
Twice a year, ideally in spring and fall, is recommended to check for damage, loose panels, or signs of water intrusion.
Can I repair siding damage myself?
Minor repairs, like replacing a damaged panel, might be manageable for DIY enthusiasts with the right tools and materials. However, extensive damage often necessitates professional assistance.
What is the best siding for coastal areas prone to hurricanes?
Fiber cement and metal siding generally offer superior wind and impact resistance, making them suitable choices for hurricane-prone regions.
How do I clean different types of siding?
Cleaning methods vary. Vinyl siding can be cleaned with a mild detergent solution and a soft brush. Fiber cement and metal may require a pressure washer (low pressure) but always check manufacturer recommendations.