Vinyl Siding Cost Per Square Foot A Comprehensive Guide
Transforming your home’s exterior with vinyl siding offers a blend of aesthetic appeal and long-term durability. However, understanding the associated costs is crucial for successful budgeting and project planning. This guide delves into the multifaceted world of vinyl siding pricing, exploring the factors that influence the cost per square foot, from material selection and labor expenses to regional variations and project complexity.
We’ll equip you with the knowledge to make informed decisions and achieve your dream home exterior within your budget.
From the initial estimate to the final installation, we’ll cover everything you need to know. We’ll examine the various types of vinyl siding available, their respective price points, and the advantages and disadvantages of each. We will also provide practical advice on finding reputable contractors and navigating the often-complex process of obtaining accurate cost estimates.
Factors Influencing Vinyl Siding Cost
The cost of vinyl siding installation is influenced by a variety of factors, extending beyond simply the price per square foot. Understanding these contributing elements is crucial for accurate budgeting and informed decision-making. This section will delve into the key aspects that impact the overall expense of your project.
Material Quality Impacts on Price
Higher-quality vinyl siding generally translates to a higher price per square foot. Premium brands often utilize thicker vinyl, enhanced UV protection, and more robust color pigments, resulting in greater durability and longevity. These features justify the increased cost, as they offer superior resistance to fading, impact damage, and warping, ultimately reducing long-term maintenance and replacement expenses. Conversely, less expensive options may compromise on these features, leading to a shorter lifespan and potential for premature degradation.
Siding Thickness and Cost
Vinyl siding thickness is directly correlated with its strength and durability. Thicker siding, typically measured in mils (thousandths of an inch), tends to be more resistant to dents and damage, resulting in a higher initial cost. A thicker profile often translates to a more substantial and realistic appearance, enhancing the aesthetic appeal of the home. Thinner siding, while more affordable upfront, may be more susceptible to damage and require more frequent repairs or replacements.
For example, a siding thickness of 40 mils is generally considered a good balance of cost and durability, while thicker options, such as 50 mils or more, provide enhanced protection.
Labor Costs in Vinyl Siding Installation
Labor costs constitute a significant portion of the overall project expense. The complexity of the project, including factors like the house’s shape, the presence of intricate trim work, and the need for specialized techniques, all influence the time and skill required for installation. Experienced installers command higher wages, reflecting their expertise and efficiency. Factors such as the geographic location and prevailing labor rates in the area further contribute to labor cost variability.
For example, in regions with a high cost of living, labor rates for skilled tradespeople tend to be higher.
Regional Variations in Vinyl Siding Pricing
Pricing for vinyl siding and installation can vary considerably depending on the geographic location. Factors such as local material availability, transportation costs, and prevailing labor rates in the region all play a role. For instance, areas with a high concentration of vinyl siding manufacturers may experience lower material costs compared to regions where materials need to be shipped over long distances.
Similarly, regions with a high demand for skilled labor may have higher installation costs. As an illustration, a project in a densely populated urban area may cost significantly more than a similar project in a rural area.
Project Complexity and Cost
Intricate designs, such as those incorporating numerous angles, curves, or specialized trim pieces, will invariably increase the overall project cost. Difficult terrain, such as steep slopes or uneven surfaces, can also add to the complexity and labor time required for installation, resulting in higher expenses. Projects requiring significant preparation work, such as the removal of existing siding or extensive repairs to the underlying structure, will also increase the overall cost.
For example, a home with many dormers or complex architectural features will require more time and expertise, leading to a higher final price.
Comparison of Vinyl Siding Types
Type | Price Range/sq ft | Features | Pros/Cons |
---|---|---|---|
Standard | $2 – $4 | Basic thickness, limited color options, standard warranty | Pros: Affordable; Cons: Shorter lifespan, may fade or dent easily. |
Premium | $4 – $7 | Thicker vinyl, wider color selection, enhanced UV protection, longer warranty | Pros: Durable, attractive, longer lifespan; Cons: Higher initial cost. |
Insulated | $6 – $10 | Includes foam insulation backing, improved energy efficiency | Pros: Energy savings, enhanced sound insulation; Cons: Highest initial cost, may require specialized installation. |
Cost Breakdown
Understanding the cost of vinyl siding installation involves separating the expenses into two primary components: materials and labor. The proportion of each significantly impacts the overall project cost, and this breakdown helps homeowners make informed decisions regarding budgeting and potential DIY versus professional installation.The relative costs of materials and labor can fluctuate based on factors like geographic location, the complexity of the project, and the chosen contractor or supplier.
However, a general understanding of the typical cost allocation provides a valuable framework for planning.
Material Costs
Materials typically account for approximately 30-40% of the total vinyl siding installation cost. This includes the vinyl siding panels themselves, along with necessary components such as trim, flashing, starter strips, J-channels, and fasteners. The price per square foot of siding varies depending on the quality, style, and manufacturer. Higher-end options, featuring enhanced durability, color stability, and thicker profiles, will naturally command a higher price.
For example, a basic vinyl siding might cost $1-$3 per square foot, while premium options could range from $3-$6 or more. The additional materials, like trim pieces, further add to the overall material cost. A homeowner should budget accordingly, factoring in the chosen siding’s quality and any additional features.
Labor Costs
Labor costs constitute the larger portion of the total expense, generally ranging from 60-70%. This encompasses the time and expertise of the installation crew, which includes tasks such as measuring, preparing the walls, installing the siding, and completing finishing touches. The labor cost is influenced by factors like the house’s size, the complexity of the project (e.g., intricate architectural details), and the prevailing wage rates in the region.
Experienced and reputable installers often charge a higher hourly or per-square-foot rate than less experienced contractors. Furthermore, the need for specialized equipment or scaffolding can also increase the labor costs.
Professional vs. DIY Installation
While DIY installation can seem appealing to save on labor costs, it’s crucial to weigh the potential drawbacks. Professional installers possess the experience and skill to ensure a proper, long-lasting installation. Mistakes made during DIY installation can lead to future problems, such as water damage, inefficient insulation, or even structural issues, potentially exceeding the initial savings in the long run.
Furthermore, professional installers are typically insured, protecting the homeowner from potential liability. The decision between professional and DIY installation involves assessing personal skills, time availability, and the willingness to accept potential risks versus cost savings.
Sample Budget for a 1000 sq ft House
This sample budget provides a general estimation. Actual costs may vary depending on the factors previously discussed.
Cost Category | Estimated Cost | Percentage of Total Cost |
---|---|---|
Materials (Vinyl Siding, Trim, Fasteners, etc.) | $2,000 – $4,000 | 30-40% |
Labor (Installation, Preparation, Cleanup) | $4,000 – $7,000 | 60-70% |
Total Estimated Cost | $6,000 – $11,000 | 100% |
Estimating Vinyl Siding Costs
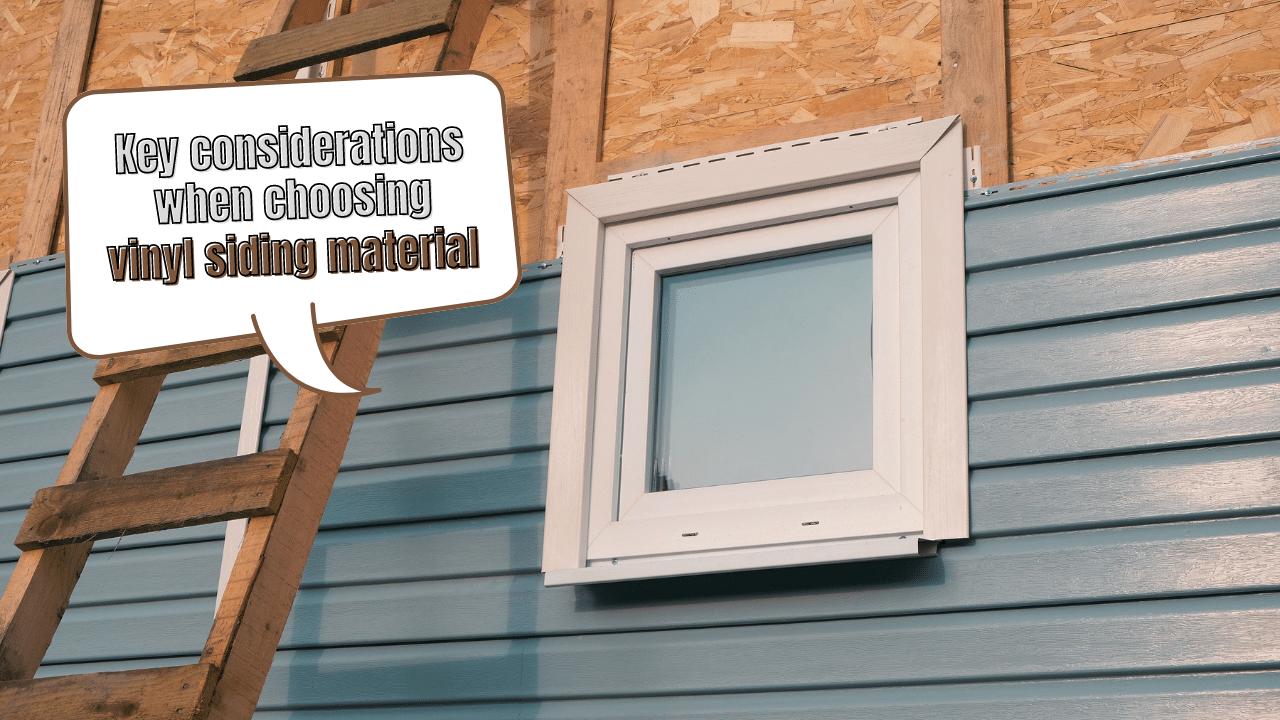
Accurately estimating the cost of vinyl siding is crucial for successful project planning and budgeting. This involves more than just calculating the square footage; it requires a comprehensive understanding of various factors and potential cost overruns. This section details methods for calculating material needs, estimating total project costs, and incorporating additional expenses.
Calculating House Square Footage for Siding
Determining the square footage of your house’s exterior walls is the first step in estimating vinyl siding costs. This calculation excludes areas like windows, doors, and other non-siding surfaces. Several methods can be employed. One common approach involves measuring the length and height of each wall, calculating the area of each wall (length x height), and then summing the areas.
Remember to subtract the areas of windows and doors from the total wall area. Another approach is to use a digital measuring tool and aerial photography. This can give you a reasonably accurate measure of the exterior wall surface area. A third method involves consulting architectural drawings if available; these plans often include precise measurements of the exterior walls.
Always double-check your measurements to ensure accuracy. For example, a house with four walls, each measuring 20 feet by 10 feet, has a total wall area of 800 square feet (20ft x 10ft x 4 walls = 800 sq ft). However, remember to deduct areas covered by windows and doors.
Estimating Total Project Costs
Several approaches exist for estimating the total cost of a vinyl siding project. Using online calculators provides a quick initial estimate, but these tools often lack the nuance of a professional assessment. Inputting your house’s square footage and other relevant details (e.g., siding type, complexity of the job) will yield a preliminary cost range. However, online calculators often do not account for regional variations in labor costs or material pricing.
Directly contacting contractors is a more reliable method. Obtain multiple bids from reputable contractors to compare pricing and services. A detailed quote should Artikel labor costs, material costs, permits, waste disposal, and any other associated expenses. This provides a more accurate representation of the total project cost than an online calculator. For instance, if an online calculator estimates $5,000, but a contractor’s bid comes in at $7,000, the contractor’s bid is likely more accurate due to their on-site assessment and inclusion of all costs.
Common Cost Overruns and Mitigation Strategies
Unexpected costs can significantly impact a vinyl siding project. Common overruns include unforeseen damage to underlying sheathing, requiring costly repairs before siding installation. Another frequent issue is the discovery of rotted wood or other structural problems. Unforeseen complications during installation, such as unexpected obstacles beneath the existing siding, can also lead to cost increases. Mitigation strategies include thorough pre-installation inspections, obtaining multiple bids to compare thoroughness, and building a contingency buffer into your budget.
A 10-15% contingency fund can help absorb unexpected costs and prevent project delays. For example, if the initial estimate is $7,000, adding a 10% contingency would bring the total budget to $7,700, providing a safety net for unexpected expenses.
Incorporating Additional Costs into the Estimate
Beyond material and labor, several additional costs should be factored into your estimate. Permits are usually required for exterior home renovations and vary in cost depending on location and project scope. Waste removal fees also need to be considered; proper disposal of old siding and other construction debris is essential. If you require specialized equipment for the project, such as scaffolding or a dumpster rental, include these expenses as well.
For instance, permits might cost $300-$500, waste removal $200-$500, and equipment rental $100-$300, depending on the project size and location. These additional costs should be included in your total project budget to avoid surprises during the project.
Vinyl Siding Styles and Their Costs
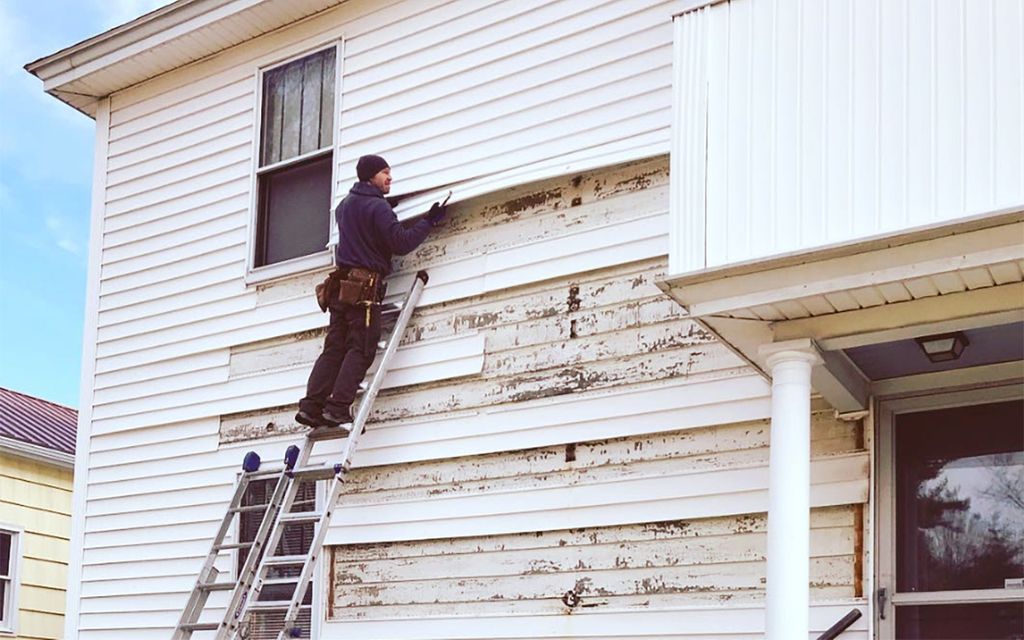
Choosing the right vinyl siding style significantly impacts the overall cost of your project. Different styles offer varying degrees of complexity in installation and material requirements, leading to fluctuations in price. Understanding these differences allows for informed budgeting and selection.
Vinyl siding styles broadly fall into categories such as clapboard, shingle, and shake, each with its own aesthetic appeal and price point. The complexity of the profile, the need for additional trim pieces, and the overall labor involved all contribute to the final cost.
Vinyl Siding Profile Examples and Price Ranges
The price of vinyl siding is heavily influenced by its profile. Simpler profiles, such as standard clapboard, generally cost less than more intricate designs. Below are examples illustrating this cost variation. These prices are approximate and can vary based on location, installer, and material quality.
Siding Profile | Price Range per Square Foot (USD) | Description |
---|---|---|
Standard Clapboard | $1.50 – $3.00 | A classic, straight-edged profile; simple installation. |
Dutch Lap | $2.00 – $4.00 | Features an overlapping design, creating a more dimensional look. |
Shingle | $3.00 – $5.00 | Imitates the look of wood shingles; more complex installation. |
Shake | $4.00 – $6.00 | Mimics the rough-hewn texture of wood shakes; requires specialized installation. |
Vertical | $2.50 – $4.50 | Provides a modern, clean look; installation may vary in complexity depending on design. |
Color Choices and Their Impact on Cost
While the base cost of vinyl siding is primarily determined by the profile, the chosen color can also influence the final price. Solid colors are typically less expensive than those with intricate patterns or wood-grain textures. Premium colors, such as deep blues or rich browns, may also command a slightly higher price due to increased manufacturing complexity or specialized pigment requirements.
For example, a standard white clapboard might cost less than a custom-mixed deep green.
Vinyl Siding Finishes and Cost Implications
The finish of the vinyl siding also plays a role in the overall cost. Different finishes offer varying levels of durability, maintenance requirements, and aesthetic appeal. This table illustrates the cost implications of different finishes.
- Smooth Finish: This is the most basic and generally the least expensive option. It offers a clean, modern look but may show scratches more easily than textured finishes. Cost typically falls within the lower end of the price range for a given profile.
- Textured Finish: Textured finishes, such as those mimicking wood grain, are more expensive than smooth finishes. The added texture provides a more realistic appearance and often better hides minor imperfections. This increased complexity in manufacturing contributes to the higher cost.
- Embossed Finish: Embossed finishes add a further layer of detail and realism, often mimicking the look of natural wood with deep grooves and textures. This is typically the most expensive finish option due to its intricate manufacturing process.
Finding Reliable Contractors
Choosing the right contractor is crucial for a successful vinyl siding project. A reputable contractor ensures quality workmanship, adherence to timelines, and proper handling of potential issues. Carefully vetting potential contractors will save you time, money, and potential headaches down the line.Finding a qualified and trustworthy contractor involves a multi-step process that goes beyond simply checking online reviews.
Thorough research and verification are essential to protect your investment and ensure a positive experience.
Obtaining Multiple Quotes
Before committing to any contractor, it’s essential to obtain at least three quotes. This allows for a fair comparison of pricing, services offered, and overall value. Ensure that each quote includes a detailed breakdown of costs, materials, and labor, enabling a clear apples-to-apples comparison. Significant discrepancies in pricing should prompt further investigation to understand the underlying reasons.
For example, one quote might be significantly lower due to using inferior materials or employing less experienced workers.
Reviewing Contractor Licenses and Insurance
Verifying a contractor’s licensing and insurance is paramount. A valid license demonstrates that the contractor has met the minimum requirements of your local jurisdiction and is authorized to perform the work. This also offers a level of consumer protection. Adequate insurance, including general liability and workers’ compensation, protects you from financial responsibility in case of accidents or damages during the project.
Request copies of their license and insurance certificates and verify their validity with the relevant issuing authorities. Failing to do so could leave you financially responsible for accidents or damages on your property.
Verifying Contractor References and Reviews
Contacting previous clients to inquire about their experiences is a valuable step in the contractor selection process. Ask detailed questions about the contractor’s professionalism, adherence to schedules, quality of work, and how they handled any unforeseen problems. Online reviews on platforms like Angie’s List, Yelp, or HomeAdvisor can provide additional insights, but remember to critically evaluate the reviews and consider the overall pattern of feedback.
A few negative reviews are not necessarily a deal-breaker, but a consistent pattern of negative feedback should raise concerns. Look for contractors with a history of positive feedback and a demonstrated commitment to customer satisfaction.
Visual Representation of Cost Factors
A clear visual representation can effectively communicate the complex interplay of factors influencing vinyl siding costs. Using a well-designed chart or diagram simplifies the understanding of how these elements combine to determine the final price per square foot.A bar chart, for example, would effectively illustrate this. The chart’s horizontal axis would represent the various cost factors, such as material cost, labor cost, permits, and waste removal.
The vertical axis would represent the cost in dollars per square foot. Each factor would be represented by a separate bar, with its height corresponding to its contribution to the overall cost. The bars could be color-coded for better visual distinction. A final, larger bar could represent the total cost per square foot, clearly showing the sum of the individual cost components.
The chart’s title would be “Breakdown of Vinyl Siding Cost per Square Foot,” and a clear legend would identify each bar’s meaning. The chart’s size would be large enough to ensure readability, possibly a standard A4 size or larger if necessary for detailed presentation.
Vinyl Siding Styles and Their Relative Costs
A comparative illustration of vinyl siding styles and their associated costs can be presented through a combination of visual and textual elements. This visual aids in decision-making for homeowners.Consider a series of rectangular boxes, each representing a different vinyl siding style (e.g., clapboard, shingle, Dutch lap). The size of each box could directly correlate to its average cost per square foot; a larger box representing a more expensive style.
Within each box, a smaller inset could display a simplified visual representation of the siding style. For instance, the clapboard box would show a simple image of vertical clapboards, while the shingle box would show overlapping shingle patterns. Beneath each box, the name of the style and its approximate cost range (e.g., $3-$5 per square foot) could be clearly labeled.
This visual comparison, using size to represent cost and small images for style identification, provides a concise and easily understandable overview of different siding options and their relative price points. The overall arrangement would be neat and organized, potentially in a grid-like format for easy comparison.
Concluding Remarks
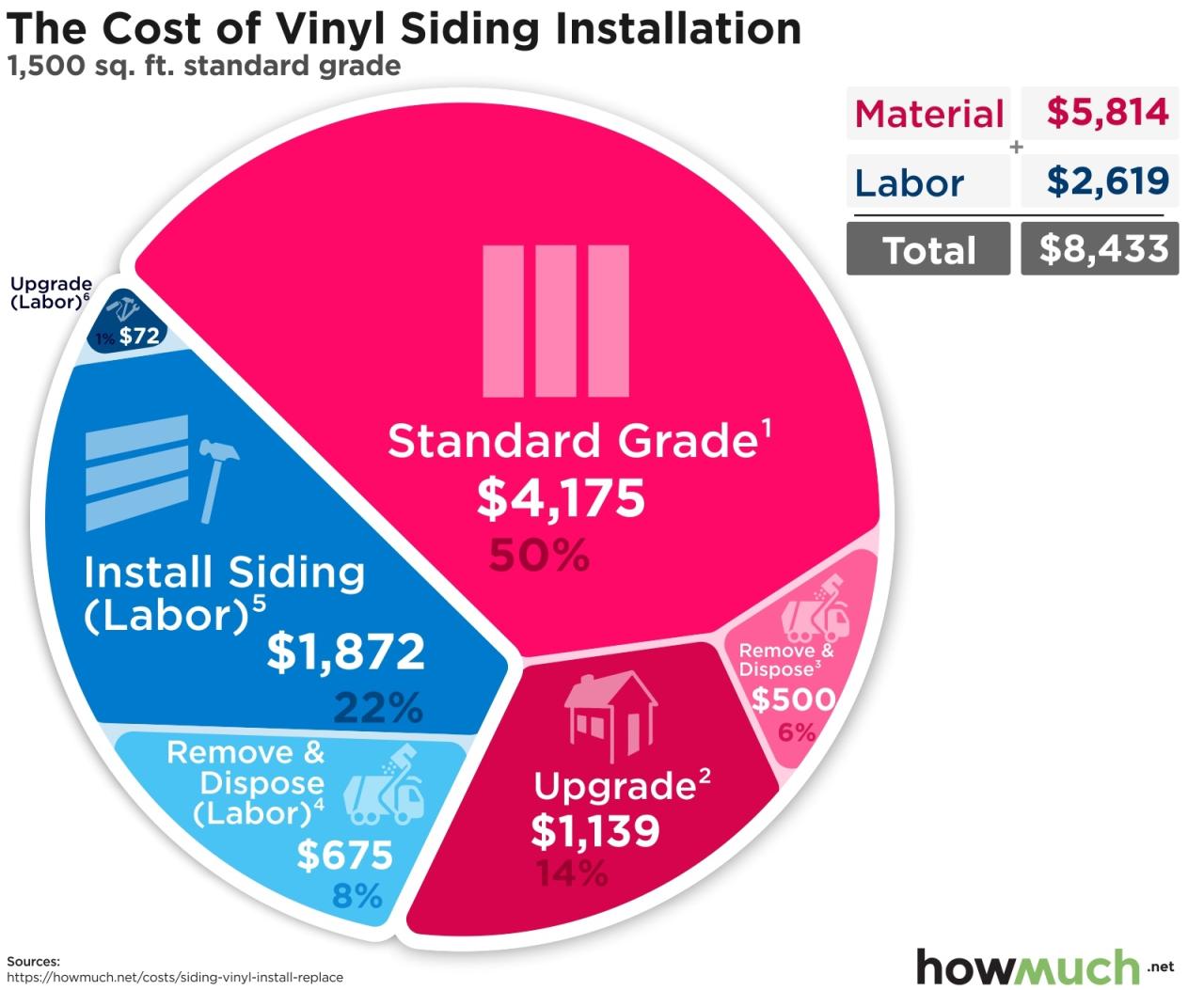
Ultimately, the cost of vinyl siding per square foot is a variable influenced by a complex interplay of factors. By understanding these factors—material quality, labor costs, regional differences, and project specifics—you can develop a realistic budget and make informed decisions. Remember to obtain multiple quotes from reputable contractors, thoroughly review contracts, and factor in potential cost overruns to ensure a smooth and successful home improvement project.
With careful planning and the right information, you can achieve a stunning and durable exterior without exceeding your financial limits.
Question Bank
What is the average lifespan of vinyl siding?
Vinyl siding typically lasts 20-50 years, depending on quality, installation, and environmental factors.
Can I install vinyl siding myself?
While DIY installation is possible, professional installation is generally recommended for optimal results and warranty coverage. Improper installation can lead to problems like water damage.
Does the color of vinyl siding affect its price?
Some colors, especially those requiring more complex manufacturing processes, may be slightly more expensive than others.
What are common hidden costs associated with vinyl siding installation?
Hidden costs can include permits, waste removal, and unforeseen repairs to underlying structures.
How important is choosing a reputable contractor?
Choosing a reputable contractor is crucial to ensure quality workmanship, warranty protection, and adherence to building codes.